" Working across the whole of the Middle east "
ISEKI MICROTUNNELLING
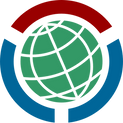
Part of the Target Trenchless Group ( Email : info@targettrenchless.com )
Micro Tunneling Middle East
Micro Tunneling Middle East
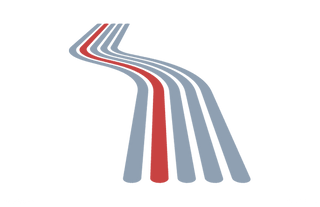

cctv middle east, cctv Saudi Arabia, cctv oman, cctv abu dhabi, cctv Kuwait, cctv Bahrain, cctv middleast, cctv Saudi Arabia, cctv oman, cctv abu dhabi, cctv Kuwait, cctv Bahrain cctv middle east, cctv Saudi Arabia, cctv oman, cctv abu dhabi, cctv Kuwait, cctv Bahrain, cctv middleast, cctv Saudi Arabia, cctv oman, cctv abu dhabi, cctv Kuwait, cctv Bahrain cctv middle east, cctv Saudi Arabia, cctv oman, cctv abu dhabi, cctv Kuwait, cctv Bahrain, cctv middleast, cctv Saudi Arabia, cctv oman, cctv abu dhabi, cctv Kuwait, cctv Bahrain cctv middle east, cctv Saudi Arabia, cctv oman, cctv abu dhabi, cctv Kuwait, cctv Bahrain, cctv middleast, cctv Saudi Arabia, cctv oman, cctv abu dhabi, cctv Kuwait, cctv Bahrain cctv middle east, cctv Saudi Arabia, cctv oman, cctv abu dhabi, cctv Kuwait, cctv Bahrain, cctv middleast, cctv Saudi Arabia, cctv oman, cctv abu dhabi, cctv Kuwait, cctv Bahrain cctv middle east, cctv Saudi Arabia, cctv oman, cctv abu dhabi, cctv Kuwait, cctv Bahrain, cctv middleast, cctv Saudi Arabia, cctv oman, cctv abu dhabi, cctv Kuwait, cctv Bahrain cctv middle east, cctv Saudi Arabia, cctv oman, cctv abu dhabi, cctv Kuwait, cctv Bahrain, cctv middleast, cctv Saudi Arabia, cctv oman, cctv abu dhabi, cctv Kuwait, cctv Bahrain cctv middle east, cctv Saudi Arabia, cctv oman, cctv abu dhabi, cctv Kuwait, cctv Bahrain, cctv middleast, cctv Saudi Arabia, cctv oman, cctv abu dhabi, cctv Kuwait, cctv Bahrain cctv middle east, cctv Saudi Arabia, cctv oman, cctv abu dhabi, cctv Kuwait, cctv Bahrain, cctv middleast, cctv Saudi Arabia, cctv oman, cctv abu dhabi, cctv Kuwait, cctv Bahrain cctv middle east, cctv Saudi Arabia, cctv oman, cctv abu dhabi, cctv Kuwait, cctv Bahrain, cctv middleast, cctv Saudi Arabia, cctv oman, cctv abu dhabi, cctv Kuwait, cctv Bahrain cctv middle east, cctv Saudi Arabia, cctv oman, cctv abu dhabi, cctv Kuwait, cctv Bahrain, cctv middleast, cctv Saudi Arabia, cctv oman, cctv abu dhabi, cctv Kuwait, cctv Bahrain cctv middle east, cctv Saudi Arabia, cctv oman, cctv abu dhabi, cctv Kuwait, cctv Bahrain, cctv middleast, cctv Saudi Arabia, cctv oman, cctv abu dhabi, cctv Kuwait, cctv Bahrain cctv middle east, cctv Saudi Arabia, cctv oman, cctv abu dhabi, cctv Kuwait, cctv Bahrain, cctv middleast, cctv Saudi Arabia, cctv oman, cctv abu dhabi, cctv Kuwait, cctv Bahrain cctv middle east, cctv Saudi Arabia, cctv oman, cctv abu dhabi, cctv Kuwait, cctv Bahrain, cctv middleast, cctv Saudi Arabia, cctv oman, cctv abu dhabi, cctv Kuwait, cctv Bahrain cctv middle east, cctv Saudi Arabia, cctv oman, cctv abu dhabi, cctv Kuwait, cctv Bahrain, cctv middleast, cctv Saudi Arabia, cctv oman, cctv abu dhabi, cctv Kuwait, cctv Bahrain cctv middle east, cctv Saudi Arabia, cctv oman, cctv abu dhabi, cctv Kuwait, cctv Bahrain, cctv middleast, cctv Saudi Arabia, cctv oman, cctv abu dhabi, cctv Kuwait, cctv Bahrain
micro tunneling middle east, micro tunneling saudi arabia, microtunneling bahrain, micro tunneling oman, micro tunneling kuwait, micro tunneling uae, micro tunneling qatar
micro tunneling middle east, micro tunneling saudi arabia, microtunneling bahrain, micro tunneling oman, micro tunneling kuwait, micro tunneling uae, micro tunneling qatar
micro tunneling middle east, micro tunneling saudi arabia, microtunneling bahrain, micro tunneling oman, micro tunneling kuwait, micro tunneling uae, micro tunneling qatar
Thrust Boring Middle East, Iseki Microtunneling Saudi Arabia, Iseki Microtunneling Oman, Iseki Microtunneling Kuwait, Iseki Microtunneling Bahrain, Micro Tunnelling Saudi Arabia, Thrust Boring Bahrain, Directional Drilling Oman, American augers Saudi Arabia, American augers Oman Pipe Jacking Qatar, Sewer Rehab UK. Thrust Boring Middle East, Directional Drilling Saudi Arabia, Microtunneling Bahrain, HDD Oman, Thrust Boring Qatar, Thrust Boring UK. Pipe Jacking Middle East, Directional Drilling Saudi Arabia, Thrust Boring Bahrain, Thrust Boring Middle East, Iseki Microtunneling Saudi Arabia, Iseki Microtunneling Oman, Iseki Microtunneling Kuwait, Iseki Microtunneling Bahrain MT Oman, Trenchless Qatar, premier micro tunnelling UK. American Augers Oman, American augers Saudi Arabia, American augers Oman, Thrust Boring Middle East, Sewer Rehab Saudi Arabia, Auger Boring Bahrain, and Thrust Boring Oman, Thrust Boring Qatar, Thrust Boring UK. Thrust Boring Middle East, Directional Drilling Saudi Arabia, American augers Saudi Arabia, American augers Oman .Thrust Boring Bahrain, Thrust Boring Pan Gulf. Thrust Boring Middle East, Micro Tunnelling Saudi Arabia, Thrust Boring Bahrain, Directional Drilling, Oman Pipe Jacking, Qatar Sewer Rehab UK. American augers Saudi Arabia, American augers Oman ,Thrust Boring Middle East, Iseki Microtunneling Saudi Arabia, Iseki Microtunneling Oman, Iseki Microtunneling Kuwait, Iseki Microtunneling Bahrain Thrust Boring Middle East, Directional Drilling Saudi Arabia, Microtunneling Bahrain, HDD Oman, Thrust Boring Qatar, Thrust Boring UK. Pipe Jacking Middle East, Directional Drilling Saudi Arabia, Thrust Boring Bahrain, MT Oman, Trenchless Qatar, premier Microtunneling UK. Thrust Boring Middle East, Iseki Microtunneling Saudi Arabia, Iseki Microtunneling Oman, Iseki Microtunneling Kuwait, Iseki Microtunneling Bahrain Thrust Boring Middle East, Sewer Rehab, Saudi Arabia, Auger Boring Bahrain,
micro tunneling middle east,directional drilling middle east,shaft sinking middle east,pipe ramming middle east,pipe jacking middleast,
.
Target Trenchless was formed to carry out and sustain the high quality HR Solutions and Life Support Service in Kuwait, Saudi Arabia, Oman, Qatar, Oman and UAE being provided by our parent company, Target Trenchless has since 1994 supplied life support services in Kuwait, Saudi Arabia, Oman, Qatar, Oman and UAE. Specific strengths made our company successful, such as the utilization of technologies available, intimate knowledge of the environment and culture and a spirited dedication to provide the highest standard of full spectrum services in Kuwait, Saudi Arabia, Oman, Qatar, Oman and UAE to our clients in both Human Resource and Life Support spheres in Kuwait, Saudi Arabia, Oman, Qatar, Oman and UAE. Since the beginning, Target has distinguished itself in unique customer service expertise n Kuwait, Saudi Arabia, Oman, Qatar, Oman and UAE. The implementation of our Quality & Safety Management Systems (ISO 9001 / OHSAS 18001 compliant) further demonstrates our commitment to ensure consistent and exceptional quality across our diverse operations at the best values offered. At all times, our delivery of services remains focused in Kuwait, Saudi Arabia, Oman, Qatar, Oman and UAE on maintaining the highest efficiency and responsiveness in ensuring the well being of our valued customers and partners. Our privacy policy secures all information received from our customers and partners, to guarantee absolute confidentiality in Kuwait, Saudi Arabia, Oman, Qatar, Oman and UAE, honesty, transparency, integrity and loyalty which became key factors of our win-win partnership throughout the past 15 years. With long years of experience, our outstanding management capabilities make Target the best and only choice for HR Solutions and Life Support Services in Kuwait, Saudi Arabia, Oman, Qatar, Oman and UAE. We take on the responsibility for overall project management, find practical solutions to problems and develop value-added initiatives in Kuwait, Saudi Arabia, Oman, Qatar, Oman and UAE. Whether it is a green-field pilot camp supporting oil drilling operations, warehouses for logistics operations or a dining facility for the military life support services in Kuwait, Saudi Arabia, Oman, Qatar, Oman and UAE, Target has the know-how and capabilities to provide an innovative and comprehensive solution for life support services in Kuwait, Saudi Arabia, Oman, Qatar, Oman and UAE. We have an in-house team of licensed and experienced architects and engineers across all building disciplines. Our designs are functional, practical and cost-effective, taking into consideration the local conditions, availability of building materials and are based on industrial best-practices. We take on full project management for complex and fast-track projects and deliver turn-key facilities. Our services range from the planning and feasibility study stage through site preparation, civil works and on-site building assembly and life support services in Kuwait, Saudi Arabia, Oman, Qatar, Oman and UAE, to the fit-out and furnishing as well as the final commissioning and hand-over process. As the majority of our projects are of a temporary nature, we have ready options of various modular accommodation and office units as well as pre-fabricated steel frame sandwich-panel buildings for warehouses or canteens. We offer economical and practical solutions for easy to erect facilities that are re-locatable and adjustable. As part of the comprehensive solution for green-field projects Target also provides all additional camp and facility infrastructure like low-maintenance power generation and integrated electrical network, utilities lines, water supply and treatment facilities, waste water treatment plants as well as life support in Kuwait, Saudi Arabia, Oman, Qatar, Oman and UAE, HVAC as well as all required CIS and security infrastructure. As part of our mission to provide a home far from home for our clients' personnel we also construct and supply sports and entertainment facilities including phone, Internet and satellite TV services.
Key differentiating factors of our Construction services include life support services in Kuwait, Saudi Arabia, Oman, Qatar, Oman and UAE. One-stop-shop for all construction related services through our in-house capabilities Feedback and lessons learned from our camp operations and maintenance department to improve and innovate design details and construction processes. A large and experienced multinational staff and labour force. A rich background and excellent logistics capability for executing projects in very severe conditions and climates. A first class network of suppliers and subcontractors. We implement the most stringent levels of Health, Safety and Security management to prevent all incidents, injuries, and illness to our clients' and our own employees. By complying with OSHAS 18001 and ISO 22000 requirements we can surpass all Health, Safety and Security expectations. We use HACCP and OSHAS techniques to ensure that during each activity all potential hazards are identified and controlled. Our Project Managers and Camp Bosses routinely conduct risk assessments during mobilization, in order to identify and mitigate agreed risks before they occur. Life Support Services, HR Solutions
Target Trenchless life support services Kuwait, Saudi Arabia, Oman, Qatar, Oman and UAE has been with well focused efforts which had established us as the premier provider of life support in the following.
Sponsorship & Support services in Kuwait, Saudi Arabia, Oman, Qatar, Oman and UAE
Recruiting
Housing
Laundry
Recreation
Management Supervision
Transportation
We offer a full range of furnished housing with secured facilities at prime locations throughout Kuwait, Saudi Arabia, Oman, Qatar, Oman and UAE. Housing is available for short-term overnight transit accommodations and for long term lease. We are capable of housing several hundred people at a time. With our vast resources and capabilities, we also offer portable housing (pre-fabricated turnkey with furniture and utilities) available anywhere you want it to be, including needed life support services.
PI shall provide Sponsorship in Kuwait, Saudi Arabia, Oman, Qatar, Oman and UAE including the following:
Local Health Insurance
Residence Stamping Charges
Kuwait, Saudi Arabia, Oman, Qatar, Oman and UAE Ministry of Social Affairs Work Permit
Transfer of US Driving License in to Kuwait, Saudi Arabia, Oman, Qatar, Oman and UAE Driver license
Kuwait, Saudi Arabia, Oman, Qatar, Oman and UAE Civil ID
Kuwait, Saudi Arabia, Oman, Qatar, Oman and UAE medical screening & Finger Prints
Visit Visa Transfer to Work Visa Cost (Certified College Degree required)
translation (Arabic/English) & Authentication
Residence cancellation, administrative and other lfe support services in Kuwait, Saudi Arabia, Oman, Qatar, Oman and UAE
Iseki Microtunneling a History
The possibility of installing an underground channel by tunnelling rather than by digging a trench from the surface goes back thousands of years. Records exist of the qanats, a water management system for irrigation in the Middle East built some 2,700 years ago; these are still in use in Iran.
In 2500 BC, a 1,000 metre long tunnel was driven under the Euphrates to connect the Royal Palace with Temple of Baal in Babylon. The Romans and Greeks were the developers of basic techniques. For several hundreds of years these techniques constituted the state-of-the-art with little in the way of technological advances. Industrial Revolution
Tunnelling entered a period of major development in the 19th century in response to the demands of industrial development. Population movement and a shift to industry led to the construction of road, rail and canal tunnels, and also the need to install main sewer systems in cities. This is turn created a demand for tunnels locations that required a new approach.
The most famous example is the Tunnel under the Thames designed by Marc Brunel and constructed by his son Isambard Kingdom Brunel. Similar to most tunnelling jobs, it encountered problems because it was situated not far below the bed of the river in very soft, saturated soils. The work started in 1825 but was not opened to the public until 1843. Two things are significant about this tunnel; Mr Brunel introduced the concept of the tunnelling shield, and the tunnel is still in use today as part of the London underground.
The shield was a major development. Marc Brunel’s first patent for a tunnel shield was in 1818. It bears many similarities to today’s open shields including individual cells or compartments and the use of hydraulic jacks. In one version the body of the shield was advanced by the hydraulic jacks. The alternative version envisaged used hydraulics to force forward individual cells.
He originally conceived using a large circular shield, but due to manufacturing problems Marc Brunel developed a rectangular shield in 1823 to drive the large tunnel under the River Thames. The shield consisted of twelve frames each with three chambers accommodating 36 men excavating the face.
These early 19th century tunnels were built lined with brick which was laborious, slow and hazardous work. British engineers P.W. Barlow and J.H. Greathead obtained a patent on a circular shield in 1864.
Mr Greathead used it in 1869 to drive a pedestrian tunnel under the Thames without undue problems. The Barlow-Greathead shield had three major advantages – simplicity, safety and speed, introducing three major innovations that are still in use today:
-
cast iron segments to line the tunnel;
-
compressed air to keep the water at bay; and
-
a grouting pan to inject grout into the voids behind the segments.
In the late 19th century the need to speed up face excavation led to the construction of various forms of shields with mechanical cutting devices. It was J. Price in 1896 who made the main breakthrough with his patent for a shield with a cutting head for excavating the earth. It combined the Barlow-Greathead shield with a rotating cutter consisting of four spoke arms on which the cutter tools were fixed. He also incorporated tub shaped scoops onto the arms, which lifted the cuttings and dropped them onto a chute feeding muck tubs. The first use was in London clay in 1897.
These types of shields with cutting heads, tunnel linings in cast iron and compressed air to balance water table and soil inflow remained the standard approach to soft ground until 1960. There were many improvements and step changes, but the basics remained the same.
Advancing technology The second half of the 20th century saw the development of tunnel machines and the means to support and line tunnels. The modern form of the drum digger – the tunnel boring machine (TBM) – was developed in 1955 using peripheral hydraulic motors for work on a 2.69 metre segment lined tunnel, with average progress of 110 m per week. Machines of this type were used to install the London Transport Victoria Line tunnels.
A limitation, which still exists today, is that the minimum diameter that can be economically driven for a traditional tunnel is around 2,000 mm. This is created by the need to erect the lining using labour behind the advancing shield. Pressure shields
Pressure balance shields were an important development, as they were capable of working in soils by providing active soil support well below the water table. It was then no longer necessary to use compressed air, with all its dangers and drawbacks, to counterbalance the external soil and hydrostatic pressure.
Slurry machines
The concept of a slurry pressure balance shield was put forward in patents in the UK and Germany in the late 19th century. In the mid-20th century, various designs were patented including one in Germany using bentonite slurry. The first machine with a cutting wheel and hydraulic mucking was used in Japan in 1967. There were three almost simultaneous lines of development in the UK, Japan and Germany.
In the UK John Bartlett was granted a patent in 1964. A prototype was built and used on jobs in London and Mexico, but a number of problems occurred that were never satisfactorily resolved.
Japanese company Mitsubishi developed this concept into a viable system in the 1960s. After the initial successful prototype, a number of machines were built. Japanese cities are largely located on the coastal plains and the subsoil conditions are mainly alluvial deposits often with high water tables. Most cities had previously relied on night soil collection as a sewer infrastructure had not been installed. The Government decreed that all cities and towns should have sewer collection and treatment systems, with the allocation of substantial funding. The combination of need and conditions created a demand for the construction industry to install sewers in difficult alluvial ground.
A third line of development was the Hydroshield from Wayss and Freitag in Germany, introducing a rear compartment containing air under pressure that acted on the slurry. In 1972, a prototype was built and used to drive a tunnel under the port at Hamburg. Modern versions of this concept have been widely used.
Pressure balance developments
Several manufacturers started producing pressure balance machines in response to the demand. Initially the first priority was to install larger diameter lines in the bigger cities, but over time the demand turned to medium and smaller diameters.
Earth pressure balance (EPB) machines are based on the concept of a blind shield sometimes used in pipe jacking work in cohesive plastic soils. The control of the soil as it enters the chamber creates a balancing pressure. Controlled soil removal as the shield advances maintains the balancing pressure. By combining advantages of blind and slurry shields, the pressure balance shield was developed. The first commercial EPB was built by IHI in 1966 in Japan according to the Sato Kogyo design.
Early pipe jacking In parallel, but quite independently, another development was underway. This was the concept of jacking in from the drive pit pipe sections behind the cutting shield to line the tunnel. By no means was this a new concept. Records of early simple pipe jacking go back to the late 19th century in Vienna and the USA. The primary use was to install relatively short lengths of casings under rail tracks and roads. Men worked at the face excavating the soil. It would appear that many of the pipes were fitted with a leading steel cutting edge.
At this time no separate steerable shield was employed. Steering in good ground was done by excavating in front of the pipe to the course required. The devices used for jacking were most likely whatever tools were available from other applications. Reference can be found to screw jacks, ratchet jacks, air piston cylinders and hydraulic jacks. Steel and cast iron pipes were pushed in using these jacks to provide a pipe or a casing. Concrete pipes came into use from the 1920s and records show the installation of concrete pipe with diameters up to 2,400 mm. Records have been found of the isolated use of pipe jacking methods in a number of European countries in the 1930s and 1940s.
The renewed interest in pipe jacking was a natural consequence of market needs. World War II had caused great damage to European infrastructure and little in the way of replacement work had been undertaken. New infrastructure was needed to meet the demands of expanding towns and cities and rising living standards. Much of the pipeline infrastructure had to be installed under busy roads and railways and at depths where open cut was impractical. The traditional methods were no longer appropriate.
During the 1950s, individuals and companies in the UK, France, Germany and Scandinavia independently took up the pipe jacking principle and developed their own equipment and methods for work. In Germany, Ed Zublin first jacked concrete pipe in 1957 and promoted the technique both as manufacturer and contractor. Several other German contractors also entered this field. By 1970 it was estimated that 200 km of pipe had been jacked in Germany. In the UK, I reintroduced the use of pipe jacking methods in 1958, driving a casing under a main railway track near Peterborough and subsequently many other casings and flexibly jointed concrete pipes to provide sewers.
Within the USA, similar methods continued with relatively little development of technique well into the 1960s. Manufacturers’ literature in 1964 still offered fixed shields, some with hoods and shelves.
During the 1960s and 1970s, techniques were refined to form the basis of present pipe jacking methods. The most important advances included concrete pipes with rubber ring joints specially designed for jacking, shields with independent jacks to give steering corrections and the intermediate jacking station.
Pipe jacking offered a solution that allowed short crossings up to 150 m to be made in a way that was inherently safe as well as economical. The ability to tunnel smaller than traditional diameters was one advantage. Operatives could be trained more quickly in the skills for pipe jacking than in the skills required to drive a timbered heading.
To cope with differing ground conditions and meet the varying market demands in different countries, new methods were devised and equipment improved. Longer, larger bores became possible. By the late 1970s, pipe jacking was no longer confined to crossings. In Japan and Europe it was also applied to sewer installation, traditionally done by conventional trenching methods or segment lined tunnels. Mechanical cutting equipment, external lubrication and conveyer systems were introduced. Hydraulic rams, power packs and control systems were greatly improved. Contractors soon had access to more versatile shields. For long drives and more difficult ground conditions, contractors needed compact and efficient jacking rigs and intermediate jacking stations. It was these developments that allowed jacked installation to become a true cost effective tunnelling method.
Installing sewer pipes required pipe jacking to be undertaken at greater depths and in less cohesive ground conditions and over longer lengths. It prompted a demand for controllable mechanised excavation and spoil disposal. In Japan there was a large market for sewers less than 2,000 mm to be installed without disruption. The limitations of segment tunnelling prompted the development in Japan of remotely controlled miniaturised pressure balance shields.
Microtunnelling
The bringing together of remote control shields and the principle of pipe jacking created the major change in the installation of small to medium diameter tunnels and sewers. Pipe jacking was limited to man-entry sizes and cohesive or pre-treated unstable soil. Japanese manufacturers combined the two methods and used the principle of pipe jacking concrete sewer pipes in diameters greater than 1,500 mm with remote control shields that could counterbalance groundwater and soil inflow. As the demand shifted towards installing smaller diameter pipes, the Japanese developed miniaturised versions of the larger machines.
These became known as microtunnelling machines. An operator at a control panel could remotely install pipes as small as 300 mm, with workers only needed in the drive pit to add the pipe sections.
Microtunnelling – a changing definition
Obalance chambers. In a slurry machine the soil is brought to the surface by the return slurry line where it is separated out and the cleaned bentonite slurry returned into the system.
The first slurry pressure-balance microtunnelling machines were introduced in 1979. Japanese manufacturers produced hundreds of pressure balance machines of all sizes. It was estimated that there were over 3,000 machines in Japan in the eighties. However, after the big sewer projects were completed, the demand for new machines slowed down.
In the early 1980s, the West German Ministry of Research and Development funded a research project into ways of improving techniques for sewer installation. Subsequently a Japanese Iseki 600 mm machine was imported to Germany for use on the Hamburg Development Program between 1981 and 1984, where 2,750 m of small diameter sewer pipe were installed. The Hamburg project convinced a number of German manufacturers and contractors to produce their own machines and also to develop smaller ones for installing house connections. The German companies still remain the biggest users and the most important manufacturers of microtunnelling machines outside Japan. Observations
Remote control pressure balance installation for tunnels and microtunnels in the range of diameters from 300 mm–3,600 mm has become the preferred method of installation throughout the world. The inherent technical and economic advantages have more or less displaced segment tunnels below 2,500 mm. The ability to install pipes remotely and accurately from 300 mm and larger is taking over from deep open cut, which is disruptive, dangerous and dirty
In the past 25 years there have been many improvements, but the basic technology is unchanged. If one looks at the manufacturer’s literature for slurry machines being produced in the eighties, the flow diagrams and the pictures of equipment don’t look very different to those being produced today. There have, in reality, been many improvements in cutters and cutting heads, lubrication, face control, and line and level monitoring so that today’s machines have greater capability for longer and curved drives in all types of soil from hard rock to the most unstable soils with a high water table.
What is not fully appreciated is the way that the skills required to install a tunnel have changed with the advances in technology. Just 50 years ago tunnelling was a hazardous and physically demanding job for the workers. Today it is intelligence and understanding, not muscle, that are needed to operate modern equipment and even for man entry sizes workers are not required to be in the tunnel except for maintenance work. This has led to a great improvement in the safety for tunnel workers
Expertise in all forms of Trenchless Technology
micro tunneling middle east, micro tunneling saudi arabia, microtunneling bahrain, micro tunneling oman, micro tunneling kuwait, micro tunneling uae, micro tunneling qatar
